Lubrication system accessoriesmaintenance and breakdown reduction
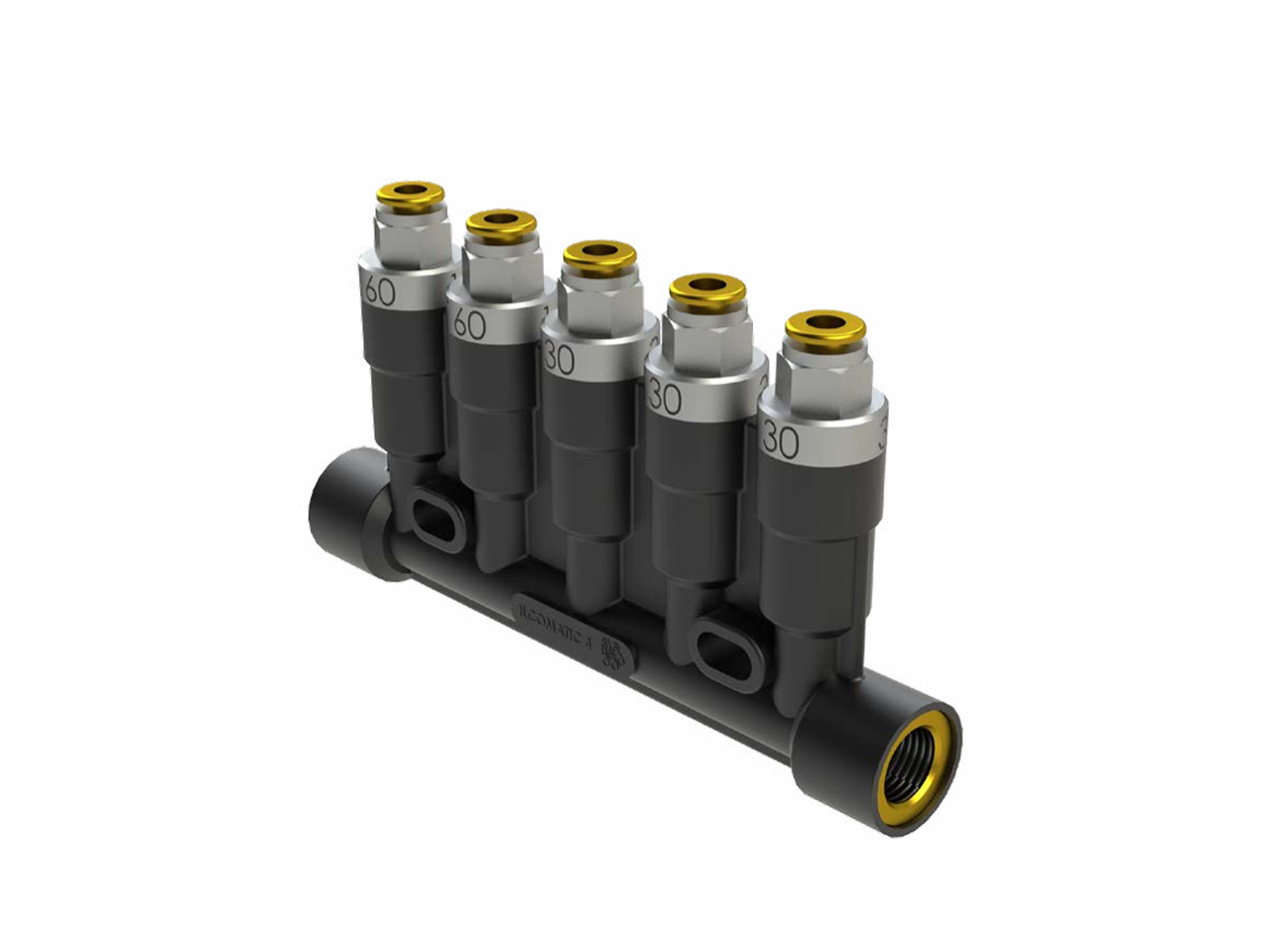
Pneumatics, Vacuum, and Lubrication
Applications
- Agricultural machinery
- Construction
- Municipal vehicles
- Industrial sector
- Mining industry
- Food industry
- Wind energy
- Printing industry

Description
The volumetric lubrication dispensers by ILC are available in two variants, ilcomatic 3 and ilcomatic 4, and can be installed on aluminum distributors or directly at the point that requires lubrication.
The dosing valves are ideal for centralized single-line lubrication systems using oil or grease. For proper operation, the line pressure should not drop below 15 bar.
These valves distribute and dose the lubricant through a pump that operates at intervals. During each lubrication cycle, a precise amount of lubricant is dispensed, ranging from a minimum of 10 mm³ to a maximum of 1000 mm³.
Features
- Lubricants: oil 32 cSt – 2000 cS, greases NGLI 000-00
- Temperatures: from 0°C to 80°C
- Seals: NBR and VITON (upon request)
- Working pressure:
- from 12 bar to 50 bar for flow rates 15-30-60-100-160-500-750-1000 mm³
- from 15 to 50 bar for flow rates 200-300 mm³
ILC's DMX and DPX are modular progressive distribution systems that accurately dispense and distribute lubricant (oil and grease) through the sequential movement of their pistons in a progressive manner.
Their modular nature allows for modification and expansion of the lubrication system, simplifying potential maintenance and providing a flexible solution to meet your needs.
The modular DMX system consists of two main parts: the bases (divided into inlet, intermediate, and final) and dosing elements available in various dosing rates.
On the other hand, the DPX modular system is composed of individual sections (inlet, intermediate, and final) with predefined dosing rates, assembled using a mounting kit.
The features of DMX dispensers include:
- Lubricants: mineral oils with a minimum viscosity of 15 cSt at the fluid's working temperature, grease with a maximum consistency of NLGI-2.
- Temperature: from -40°C to +120°C
- Working pressure: from 15 to 400 bar
- Flow rates: available pistons from 40 mm³ to 650 mm³
The features of DPX dispensers include
- Lubricants: mineral oil 46 cSt, maximum grease NLGI-2
- Temperature: from -20°C to +100°C
- Working pressure: from 15 to 300 bar
- Flow rates: from 25 mm³ to 105 mm³
Resistive dosing valves can be installed on both single-line and dual-line aluminum distributors or directly at the lubrication point. The line pressure should be between 2 and 15 bar.
These resistive dispensers are equipped with a check valve to prevent the respective lubricant-filled tubing from emptying during idle periods.
Features
- Lubricant: oil 50 and 500 cSt
- Flow rates: from 0.085 to 58.880 cc/min
- Working pressures: from 5 to 12 bar
- Temperatures: from -10°C to +60°C
Minimal lubrication involves atomizing oil with the help of compressed air. Atomization is achieved through two coaxial tubes connected to the terminal nozzle, allowing the lubricant molecules to be sprayed onto the tool.
The coaxial tube comes in a standard length of 5 meters and is made with an outer tube of 6/8 mm and an inner tube of 2.5 mm.
Upon request, we can provide tubes in different lengths and with special protections to prevent damage and for use at high temperatures.
The terminal nozzles come in various shapes to ensure proper atomization onto the tool to be lubricated.
The MIXER-X valves are air-oil mixers equipped with high-precision volumetric dosers. These valves can be assembled into up to 8 individual modules. Each module offers the ability to customize the dosing volume, with values ranging from 10 to 160 mm³ per cycle. A distinctive feature of the Mixer X is the presence of a screw for adjusting the airflow, in addition to the dosing system. The operation of the doser is monitored by an inductive sensor and a small control piston, both located internally. In the event of any obstacle that prevents the normal movement of the piston, an alarm signal is generated.
Features
- Lubricants: oil with viscosity from 16 to 220 cSt
- Flow rates: 10 - 20 - 30 - 60 - 100 -160 mm³/cycle
- Working pressure: from 10 to 40 bar
- Temperatures: from +5 to -80 C°
Advantages of dosing systems
- They prevent machine downtime, increasing production times
- They extend the life of bearings and moving parts
- No periodic maintenance is required
- Production time is maximized by significantly reducing breakdowns caused by lack of lubrication
- The system is easy and cost-effective to install
- It is possible to lubricate hard-to-reach points
Advantages of nozzles
- Increase in production
- Increase in tool lifespan
- Elimination of fumes and oil particles
Are you interested in our products?
Register to Fluid-Hub.net, the digital portal for our products.
Shop directly online and get an extra 2% discount and many other benefits!
Choose the dispenser you need and go directly to Fluid-Hub.net
Series | Average stock | Discover online availability |
---|---|---|
Ilcomatic 3 | ✅ Usually available | ⌛ Soon online |
Ilcomatic 4 | 🚚 Orderable from the supplier | ⌛ Soon online |
DMX | ✅ Usually available | ⌛ Soon online |
DPX | ✅ Usually available | ⌛ Soon online |
Resistive dispensers | ✅ Usually available | ⌛ Soon online |
MIXER X | 🚚 Orderable from the supplier | ⌛ Soon online |
Download
- Ilcomatic 3 dispensers catalogue Download Ilcomatic 3 dispensers catalogue
- Ilcomatic 4 dispensers catalogue Download Ilcomatic 4 dispensers catalogue
- DMX dispensers catalogue Download DMX dispensers catalogue
- DPX dispensers catalogue Download DPX dispensers catalogue
- MIXER X dispensers catalogue Download MIXER X dispensers catalogue
- Misting nozzles catalogue Download Misting nozzles catalogue
Why Your Fluid Mate?

Presence in the territory

Automated warehouse
To monitor the order flow with precision, accuracy and speed

Wide range of products
We offer you multiple alternatives to quickly meet your request
Specialized technical support
We study the comparisons with other brands and provide support for your project
Assembly and testing of pneumatic panels
We design, draw, assemble and test control pneumatic panels
